Fully Automatic Spot Welder For New Age Cars
What is Spot welding?
Spot welding is a resistance welding process used primarily to weld two or more metal sheets together. It is used in a wide range of industries but notably for the assembly of sheet steel vehicle bodies. This is a type of resistance welding where the spot welds are made at regular intervals on overlapping sheets of metal. Spot welding is primarily used for joining parts that are normally up to 3 mm in thickness. Thickness of the parts to be welded should be equal or the ratio of thickness should be less than 3:1.
Transformer Spot welding – The switch causes the stored energy to be dumped into the welding transformer. The welding transformer steps down the voltage and steps up the current.
Inverter Spot welding – The Global Automotive Aftermarket Body shops have now moved to the Next generation inverter type spot welders which are needed to efficiently weld the new generation steel as these Inverter type spot welder have high welding power with low power consumption.
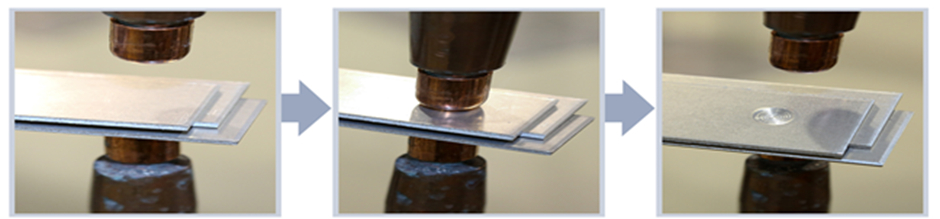
Inverter welding & Transformer welding
Parameter | Inverter Spot | Transformer Spot |
Max. Welding Amperage | 13500 / 14000 A,3 Phase 400 V 50/60 Hz | 7000/ 9000 A ,3 Phase 400 V 50/60 Hz |
Machine Type | Inverter Based | Transformer Based |
Welding Operation Mode | Fully Automatic & Manual Mode | Manual Mode |
Spot Gun | X Clamps | X Clamps |
Duty Cycle | High | Low |
Spot Gun Clamps | 3 Set of Clamps | 1 Set Clamp |
Single Side Spot Gun | Available | Available |
Multi-function modes | Available | Available |
Cooling System | Water cooled(Cooling up to end of the SPOT GUN ) | Air cooled |
Display | LED Display | LED Display |
Water Tank | Available | Not Available |
Portable | Yes | Yes |
What makes Inverter welding efficient?
Constant control of the spot-welding process : inverter technology makes it possible to achieve strict control of all welding parameters and extremely rapid reaction times in restoring optimal working conditions.
Medium frequency direct current (MFDC) : inverter technology guarantees considerable advantages compared to traditional low frequency alternating current systems
Lower absorption : DC current allows for an increase in the power factor and hence a noticeable reduction in current absorption from the power supply line.
Excellent appearance and strength of spot welds : the inverter dynamic ensures much lower working times (1ms) compared to traditional systems (20ms).
High power and compactness : inverter technology allows systems to be structured with high available currents, but with reduced overall dimensions.
Constant control of the spot-welding process : inverter technology makes it possible to achieve strict control of all welding parameters and extremely rapid reaction times in restoring optimal working conditions.
Reduced ejection of melted material : DC current ensures that regular heat transfer is reached in a much shorter time compared to AC systems; this reduces the ejection of melted material.
Below are different types of spot in various steels:-

Special Features:
- Pre- and post-heating for interventions on HSS and galvanized metals
- Automatic recognition of the arm and inserted tool
- Monitoring of mains voltage
- Automatic cooling control of machine, clamp and cables
- Regulation of approach, slope, welding and holding times
- Regulation in pulsed welding
- Automatic/manual regulation of pressure between electrodes
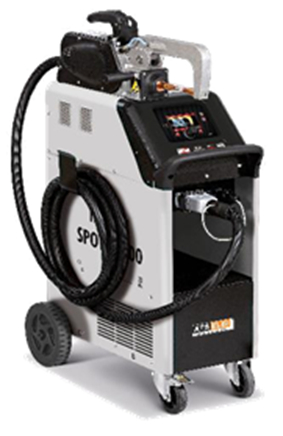