Welding and Cutting Solutions – Part 2
MIG Welding and What are they used for
Fusion welding is a process that uses heat to join or fuse two or more materials by heating them to melting point. The fusion welding processes are grouped according to the source of heat . Eg Electric arc, gas. Arc welding process is the most common process. Sometimes referred to by its subtypes Metal Inert Gas and Metal Active Gas is a welding process in which an electric arc forms between a consumable MIG wire electrode and the workpiece metal, which heats the workpiece metal, causing them to fuse.
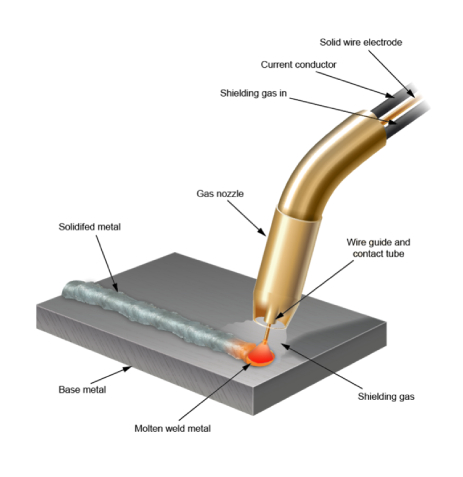
Types of MIG Welding
Stitch Welding
On lap joints where spot welder is
not available.
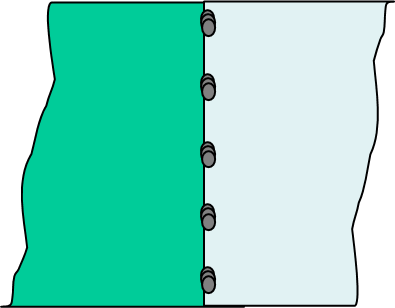
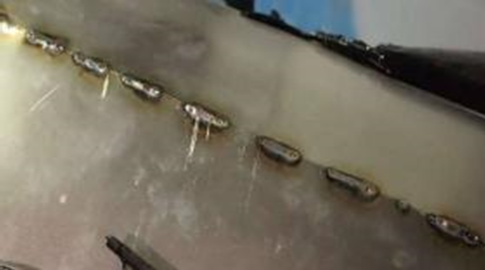
Plug Welding
On lap joints, to add strength and for reinforcement pieces
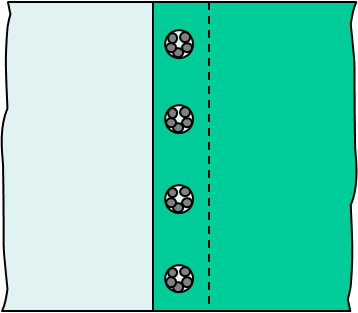
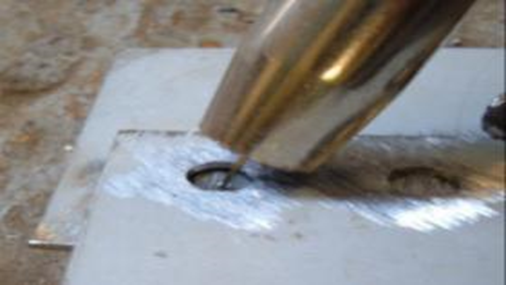
Seam Welding (Butt )
Continuous weld, for butt
joints
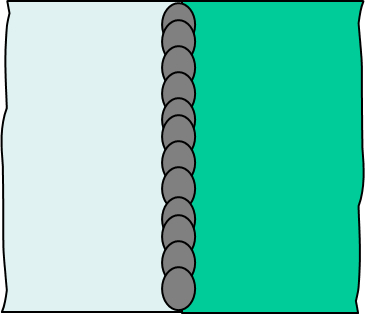
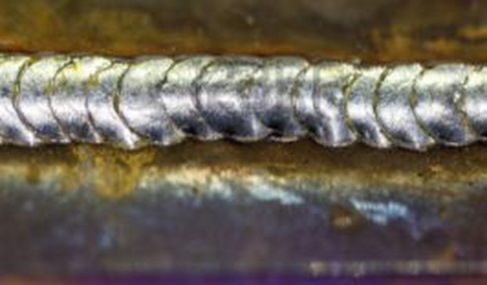
Why MIG Welding
MIG welding is the awesome process of using electricity to melt and join pieces of metal together. MIG welding is sometimes referred to as the “hot glue gun” of the welding world and is generally regarded as one of the easiest type of welding to learn
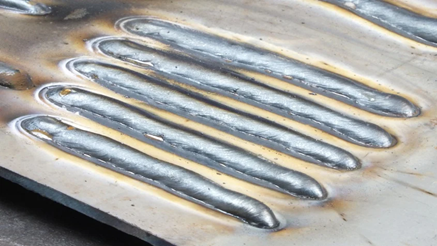
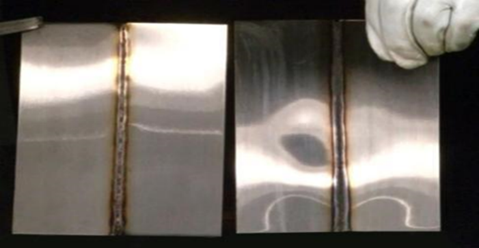
Importance of Welding
The MIG process enables the home-hobbyist, artist, farmer/rancher, motorsports enthusiast or DIY welder to make most types of fabrication and maintenance/repair welds on material from 24-gauge up to 1/2-inch thick. In addition to flexibility, many people turn to MIG welding because they’ve heard that it’s an easy process to learn. Some claim it’s no harder to use than a glue gun.
While it’s not quite that simple, it is true that most people can become competent MIG welders by following some basic advice.
- Safety first
- Metal preparation
- Equipment preparation
- Wire selection
- Gas selection
- Voltage and amperage
- Wire stick-out
- Push or pull?
- Travel angle
- Work angle
- Position
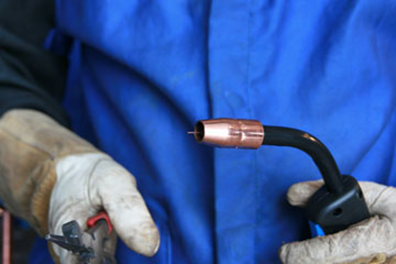
Advantages of MIG Welding
- Higher Welding Speeds
- Greater Deposition Rates
- Less Post Welding Cleaning ( e.g no slag to chip off weld)
- Better weld pool visibility
- No stub or losses or wasted man hours caused by changing electrodes
- Positional welding offers no problem when compared to other processes ( Use dip or pulsed mode of transfer)
- The process is easily automated
- No fluxes are required in most cases.
Disadvantages of MIG Welding
- Higher initial setup cost
- Atmosphere surrounding the welding process has to be stable (hence the shielding gasses), therefore this process is limited to draught free conditions
- Higher maintenance costs due to extra electronic components
- The setting of plant variables requires a high skill level Less efficient where high duty cycle requirements are necessary
- Radiation effects are more severe
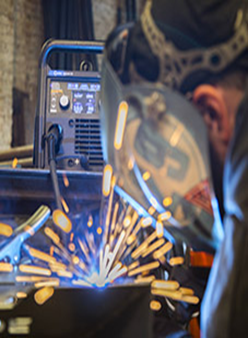